SEI Program Requirements
View and download the related infographic
DOWNLOAD INFOGRAPHIC
The SEI Certification Process
Join 150+ manufacturers who use SEI to certify over 2,500 product models. SEI staff is here to guide you through the certification process every step of the way.
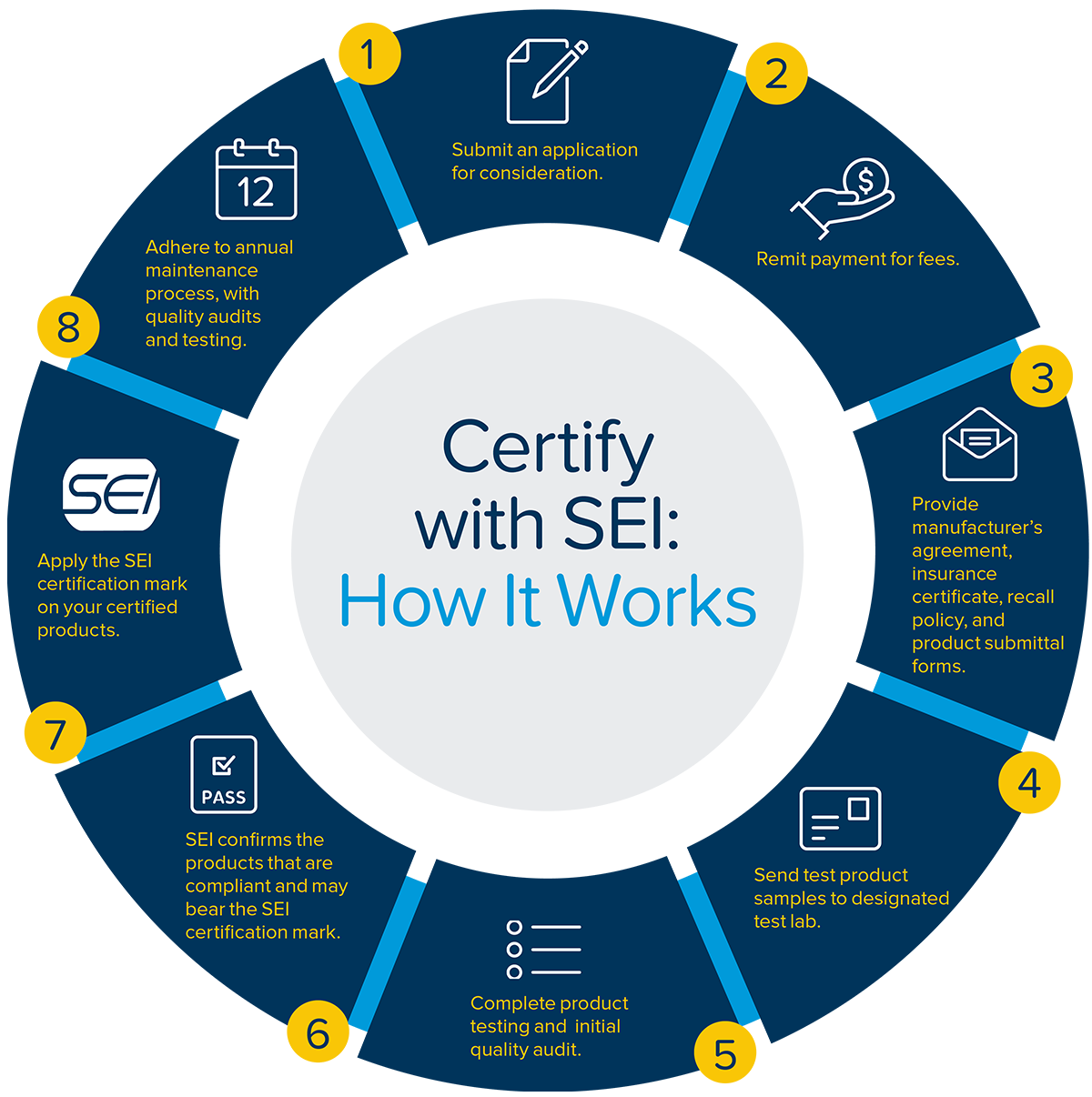
– Submit SEI certification application.
– Remit payment of all SEI fees (one-time application fee, annual participation and model fee, product testing fee, initial quality audit fee).
– Submit a copy of product liability insurance to demonstrate adequate coverage. Include endorsement form to add SEI as additional insured for products/completed operations.
– Complete and submit a product submittal form for each model that will be certified, including product description(s).
– Arrange for test samples to be sent directly to the appropriate test laboratory along with a copy of the submittal form.
– SEI completes product testing and initial quality audit.
– SEI confirms which products are compliant and may bear the SEI certification mark.
– Apply SEI mark to your product(s)
– Perform periodic testing to confirm continued compliance to applicable standard.
– Participate in annual surveillance audits to verify continued compliance of the manufacturer's quality system.
– Select samples to represent each certified model and submit to SEI laboratory for annual certification testing.
– Remit annual fees (surveillance audits, annual re-certification product testing, annual participation, annual certification per model).
– Notify SEI of any changes to the certified product or quality systems. Any changes will be assessed by SEI and the manufacturer will be notified of any required actions.
Contact us today to get started.